Roller Chain Lubrication
Roller Chain Lubrication
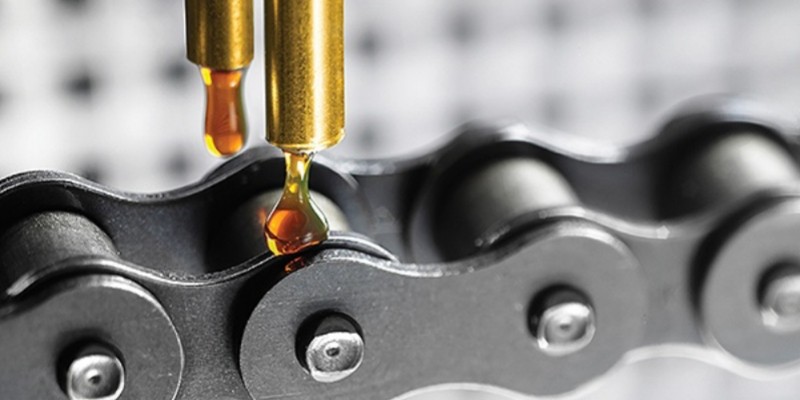
Proper industrial chain lubrication is essential for maintaining the efficiency, longevity, and reliability of industrial machinery. In various applications, from conveyor belts to heavy-duty drives, ensuring that chains are adequately lubricated can prevent downtime, reduce repair costs, and enhance overall performance.
Lubrication serves multiple purposes, including reducing friction and wear, which extends the life of chains by minimizing metal-to-metal contact. It also helps in dissipating heat, preventing corrosion, and reducing noise, thereby improving the overall operational efficiency of the machinery.
Roller Chain Lubrication Methods
Manual Lubrication
Techniques:
Applying lubricant using a brush or oil can is straightforward but labor-intensive. This method is suited for low-speed applications or where automatic systems are not feasible.
Advantages:
Cost-effective and simple.
Disadvantages:
Time-consuming and prone to human error .
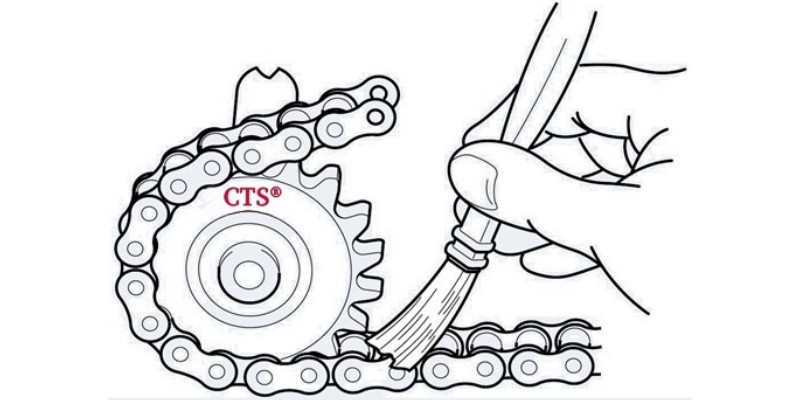
Automatic Lubrication
Dirp and Splash Methods:
These involve periodically applying oil, either through drip systems or by splashing it onto the chain. They are suitable for medium-speed operations.
Centralized System:
These systems automate the lubrication process, ensuring consistent and precise application, which is ideal for high-speed or continuous operations
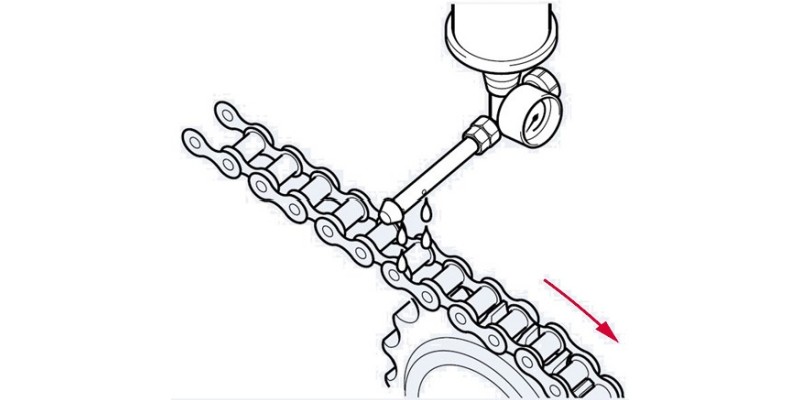
Advanced Methods
Oil Bath and Oil Disc Systems:
These methods immerse the chain in oil or use a rotating disc to distribute lubricant, providing thorough and continuous lubrication.
Force-Feed Systems:
These deliver a steady stream of lubricant directly to the chain, ideal for high-speed and high-load applications
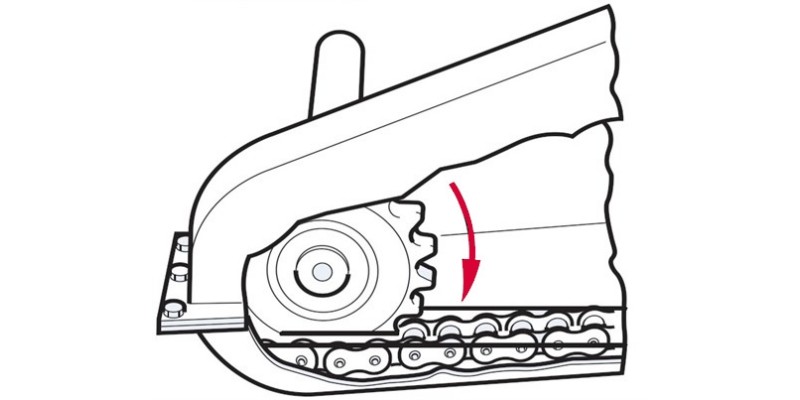
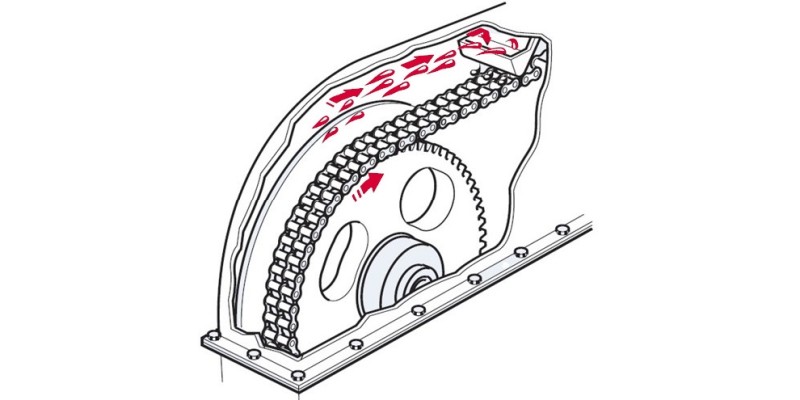
Selecting the Right Roller Chain Lubricant
Choosing the correct lubricant is crucial. Petroleum-based lubricants are economical and suitable for general purposes, while synthetic lubricants offer better performance at higher temperatures. Open-gear lubricants are effective in dusty environments where maintaining cleanliness is challenging.
Petroleum-Based Lubricants:
Affordable options for temperatures up to 250°F (120°C).
Open-Gear Lubricants:
Sticky solutions for open gears, used alongside internal petroleum-based lubricants on chain surfaces. Resistant to high pressure but can attract dust in dusty environments.
High-Temperature Lubricants:
Synthetic oils like PAOs, PAGs, or esters for conditions up to 520°F (270°C). Watch for evaporation and residue at high temps.
Extreme High-Temperature Lubricants: Solid options:
Graphite: Up to 1000°F (540°C).
MoS2: Up to 840°F (450°C).
Copper, Nickel, or Inorganic Powders:
Up to 2600°F (1425°C).
Incidental Food Contact – NSF H1 Lubricants:
Essential for potential food contact.
Dry Chain Lubricants (e.g., PTFE powder):
Protects without liquid, extending chain life up to 4 times longer.
Roller Chain Mantain
Regular inspection and Maintenance
Look for signs of poor lubrication, such as chain stretch or unusual noise. Establish a consistent lubrication schedule based on the chain’s operating conditions and follow manufacturer guidelines to ensure optimal performance.
Watch & Listen:
If roller chains become noisy or stiff, lubricate them immediately and establish a regular lubrication schedule. Use the information below to ensure you are lubricating the right areas with the best lubrication technology or product.
Chain stretch:
Chain stretch, or elongation, indicates poor lubrication, caused by internal wear and inadequate lubrication. Use a chain elongation gauge to determine when to replace the chain, typically when elongation reaches 2.5-3%. Exceeding 3% elongation increases costs, so replace the chain promptly. Temporary fixes like adjustment or removing links are ineffective, and the chain is likely to break unexpectedly. Check areas with heavy motion between the pin and bushing, such as in a chain hoist, focusing on sections under high tension.
Close tolerance:
The most common cause of chain failure is internal wear of the pin and bushing, which fit together with close tolerances. These parts bear the load and flex, functioning as the chain's "bearing" area. Regular re-lubrication of these areas is essential to prevent wear and ensure smooth operation.
CTS® | Professional Roller Chain Supplier
CTS®-ChinaTransmissionS is a professional roller chain supplier with over 14 years in the power transmission industry. Our experienced technical team always learns the latest manufacturing technology. We would be a better choice for you to build a long-term and stable cooperation with. We can provide priority service and fast response the first time. In addition, we can also offer high-quality roller chains at a competitive price.
We offer a wide range of industrial chain options: roller chains, conveyor chains, stainless steel chains, heavy-duty roller chains, double-pitch roller chains, roller chain attachments, etc.
If you have any questions about roller chains, please contact us to help you.
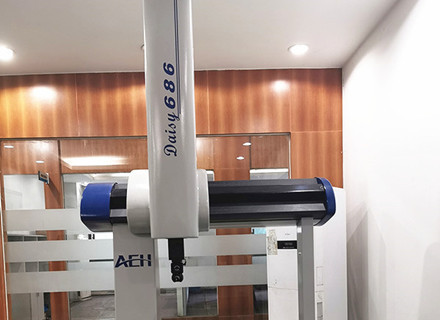
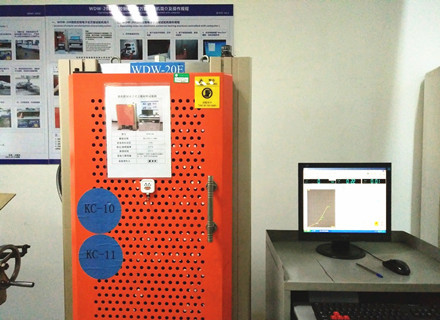
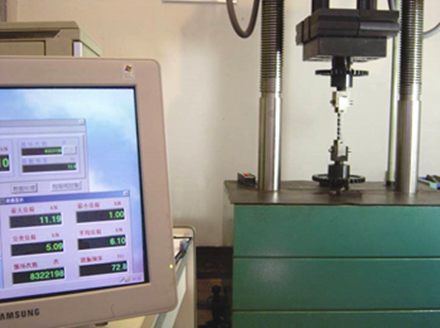
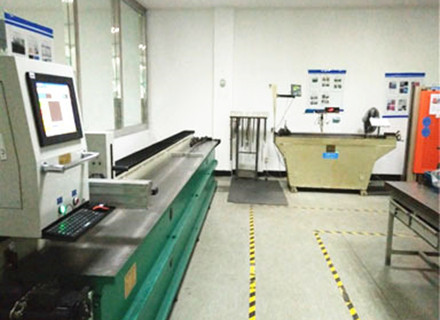
CTS® Roller Chains Test and Quality Control Equipment
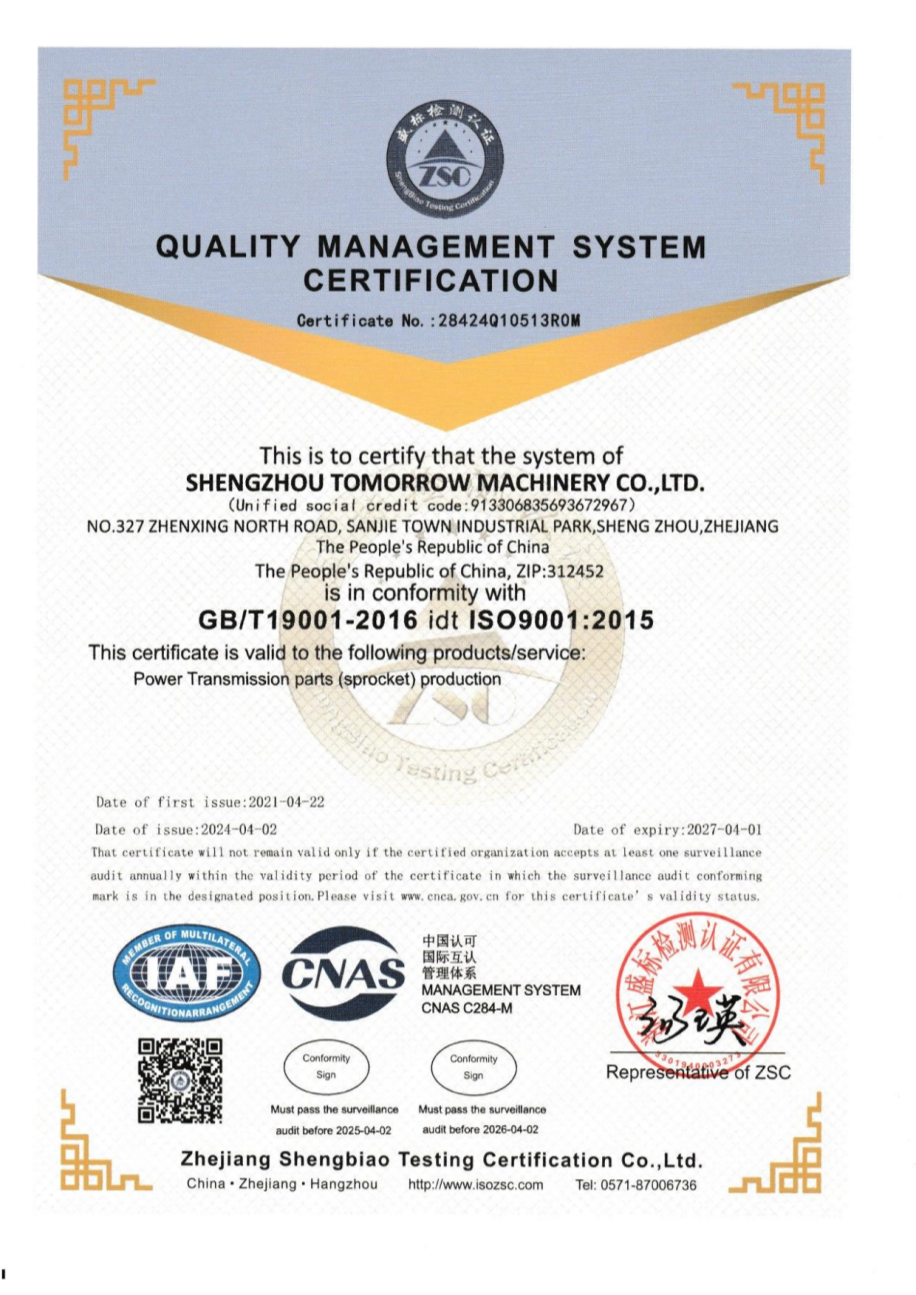
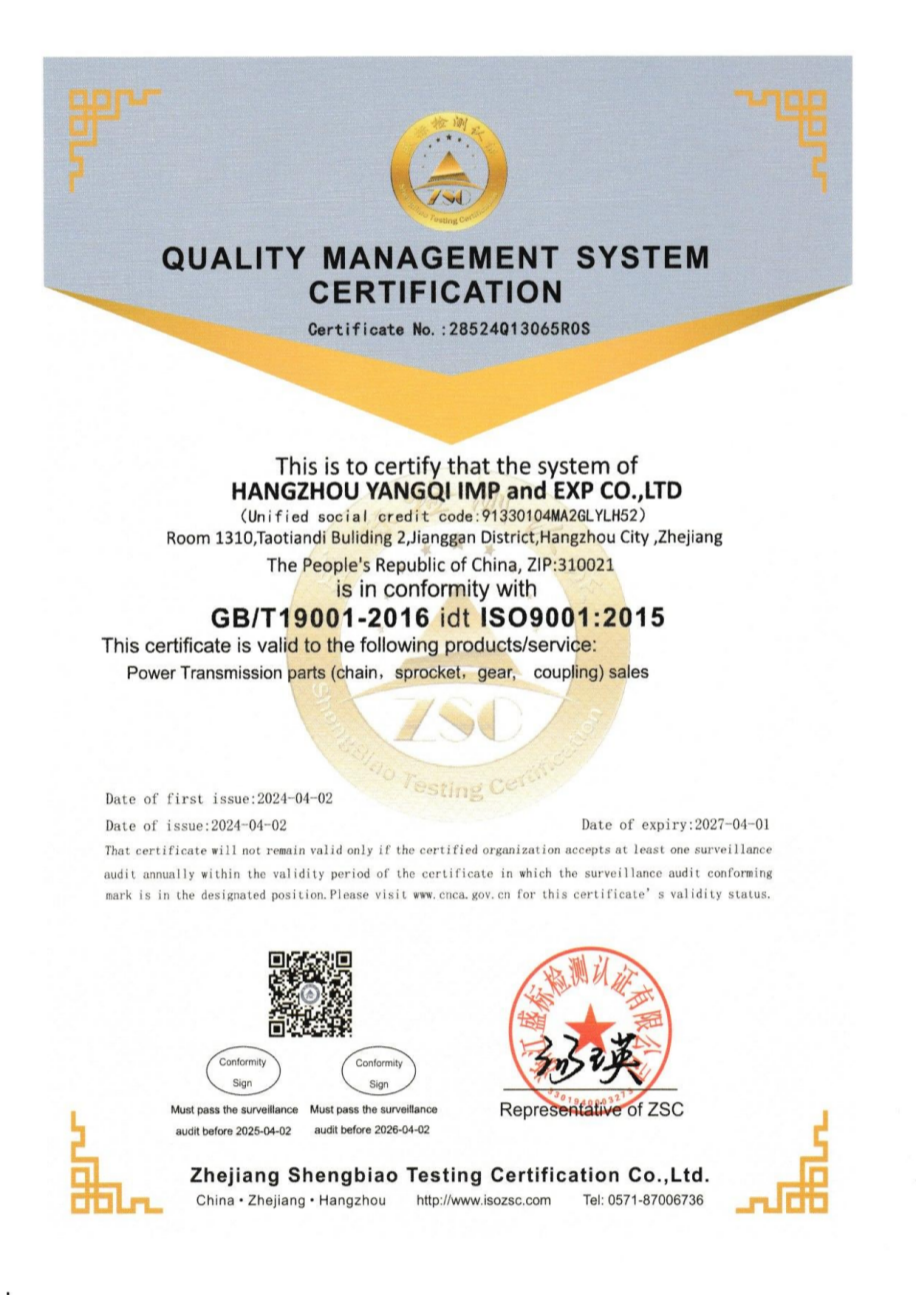
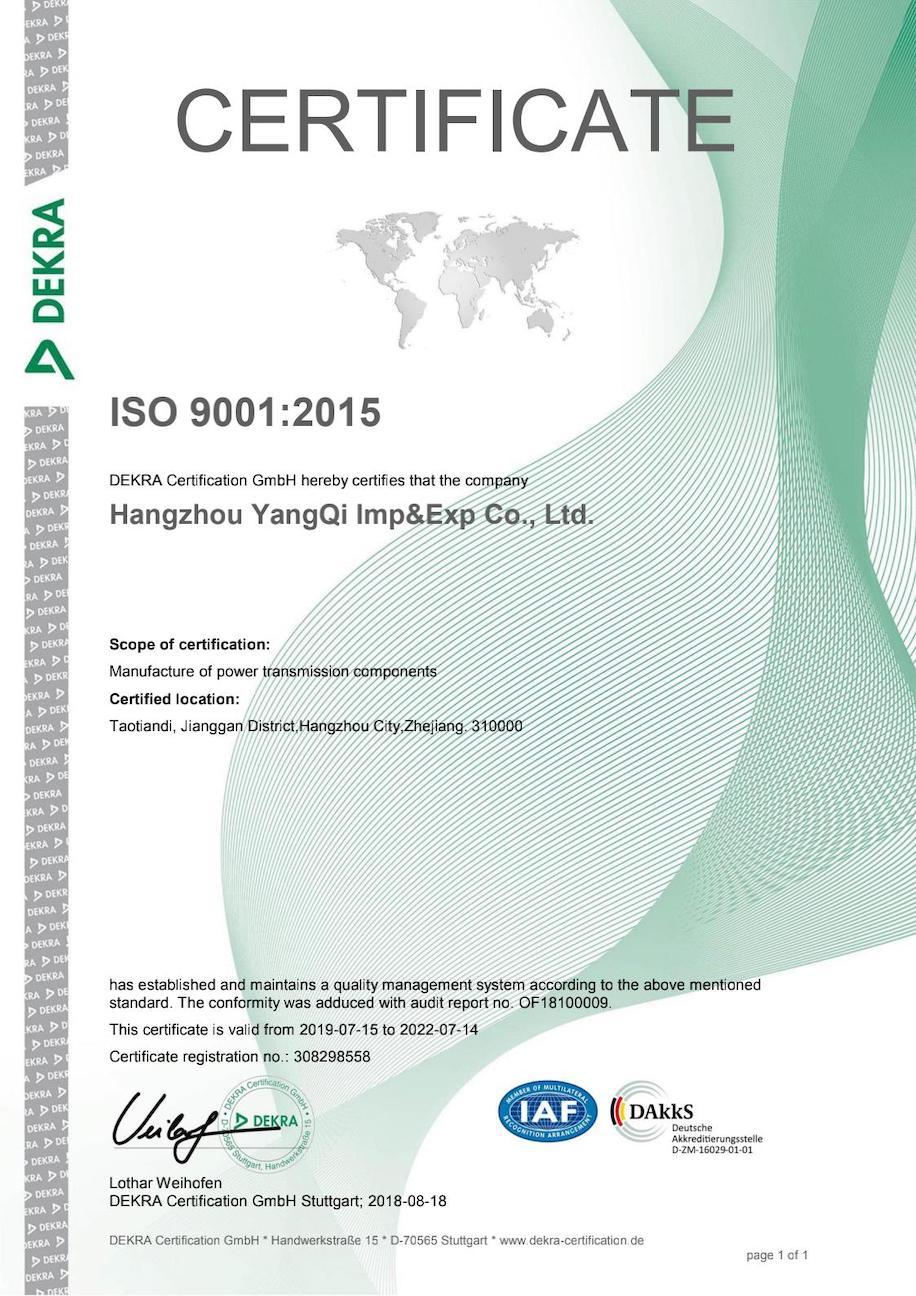
CTS® Quality Certifications