How To Choose The Right Industrial Chain Sprocket for Your Environment
Selecting the correct industrial sprocket for your equipment is crucial for efficient operation and prolonging the lifespan of both the sprocket and the machinery. The decision involves multiple factors, including load capacity, material selection, and how the sprocket will perform in specific environmental conditions. A poorly chosen sprocket can result in premature wear, frequent downtime, and higher maintenance costs. This guide will help you choose the best sprocket based on the operating environment.
Industrial Sprocket Load Capacity
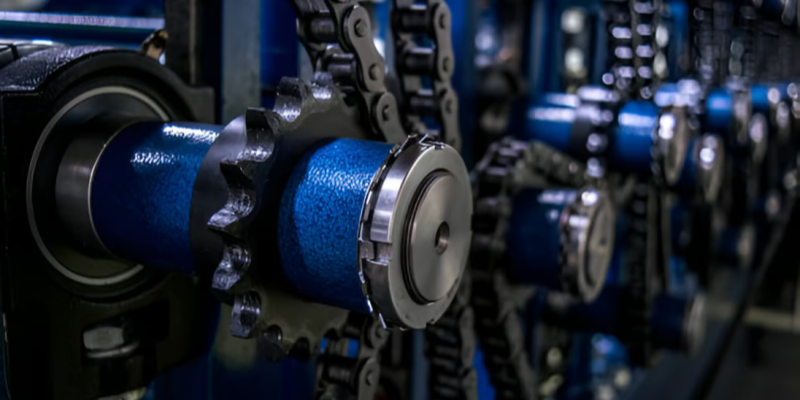
One of the most important factors is ensuring the sprocket can handle the weight it will support during operation. Heavy loads require robust materials, typically hardened steel or alloy steel, to avoid issues like deformation or failure under pressure. For lighter loads, aluminum or plastic sprockets may be more cost-effective, especially in applications where weight reduction is critical. However, selecting a sprocket with inadequate load capacity can lead to rapid wear or complete failure, which poses both operational risks and safety concerns.
Industrial Sprocket Material
Material selection is directly related to the environment in which the sprocket will be used. Each material offers unique advantages for different conditions:
Steel: Steel is widely used for its strength and durability. It is ideal for heavy-duty and high-stress environments but may rust in moist conditions unless coated.
Stainless Steel: For environments exposed to moisture, chemicals, or corrosive substances, stainless steel is the best choice due to its corrosion resistance. This material is commonly used in food processing and marine and chemical industries.
Cast Iron: Known for its cost-effectiveness and wear resistance, cast iron is often used in moderate-duty applications where budget constraints are significant.
Aluminum: Lightweight and resistant to corrosion, aluminum sprockets are used in applications where reducing the overall weight of the system is critical, such as in the automotive and aerospace industries.
Plastic and Nylon: Lightweight and corrosion-resistant, plastic or nylon sprockets are suitable for lighter loads and industries where hygiene is important, such as food processing or pharmaceuticals.
Industrial Sprocket Environmental Conditions
The operating environment plays a key role in selecting the right sprocket. Different environments pose distinct challenges, and using an inappropriate sprocket material can drastically reduce its lifespan:
Corrosive Environments: Sprockets exposed to moisture, chemicals, or constant humidity should be made from stainless steel or plastic to avoid rust and corrosion. For extreme chemical exposure, plastic sprockets offer excellent resistance.
High Temperatures: For operations in high-heat environments, heat-resistant alloys such as those used in furnaces or high-temperature conveyors are essential. Some metals degrade quickly under heat, so choosing a material like alloy steel ensures longevity.
Abrasive Conditions: In environments with dust, sand, or other abrasive particles, hardened steel or alloy sprockets are preferred because of their ability to withstand wear and tear.
Industrial Sprocket Frequency and Type of Motion
Different operating speeds and motion types have varying effects on sprocket wear. In high-speed applications, sprockets experience more wear due to friction, so hardened steel is usually recommended. On the other hand, low-speed applications may allow for the use of materials like cast iron or aluminum, which are more cost-effective but less durable in high-speed settings.
Selecting Sprockets for Specific Environments
Corrosive Environments
If the sprocket will be exposed to moisture, chemicals, or saltwater, choose a stainless steel sprocket. Stainless steel is naturally resistant to rust and corrosion, making it ideal for marine applications, food processing plants, and environments with constant exposure to cleaning agents. Plastic sprockets can also be a viable choice due to their high resistance to moisture and chemicals, but they are limited to lighter loads.
High-Temperature Conditions
Heat-resistant alloy sprockets are essential in environments with sustained high temperatures, such as industrial ovens, furnaces, or kilns. Steel sprockets may not perform well in these conditions as high temperatures can weaken the material over time, leading to rapid wear or failure.
Abrasive Conditions
In mining, construction, or other industries where sprockets are exposed to dust, sand, and abrasive materials, hardened steel sprockets are the best choice. Their ability to withstand harsh environments ensures longer operational life and reduces maintenance costs.
CTS-ChinaTransmissionS is a professional industrial chain sprocket manufacturer, if you can not choose the right chain sprocket for your equipment, Contact us, and our technicians will be happy to help you!