Zinc Plated vs Galvanized | Corrosion Resistance in Industrial Components
Choosing the right type for your application is important. Corrosion resistance, durability, and cost are key factors to consider. Among the zinc-plated and galvanized roller chains, which one should you pick? Let's know the difference between zinc-plated roller chains and galvanized roller chains to help you make an informed decision.
What is a Zinc-Plated Roller Chain?
The Zinc Plating Process
Zinc plating involves electroplating a thin layer of zinc onto the roller chain. This process creates a smooth, shiny finish that helps resist rust and corrosion in mild environments.
Key Features of Zinc-Plated Chains
Thin Coating Benefits
The thin zinc layer provides moderate protection without adding much weight. It’s ideal for applications where lightweight and flexibility are essential.
Aesthetic Appeal
Zinc-plated chains often have a polished, attractive finish. This makes them a popular choice for visible machinery or decorative applications.
What is a Galvanized Roller Chain?
The Galvanizing Process
Galvanizing typically involves dipping the chain into molten zinc, resulting in a thicker, more robust coating. This process offers superior protection against rust and corrosion.
Key Features of Galvanized Chains
Thick Coating Advantages
The thicker zinc layer provides extended durability, making galvanized chains perfect for challenging environments.
Enhanced Durability
With a rougher texture and greater resistance to wear, galvanized chains outperform zinc-plated ones in rugged settings.
Comparing Zinc-Plated and Galvanized Roller Chains
Zinc-plated Roller Chain | Galvanized Roller Chain | |
Corrosion Resistance | Resistant to corrosion | More resistant to corrosion, especially in wet or salty conditions. |
Durability | Durable | Durable, especially in heavy-duty or abrasive applications. |
Cost Difference | More budget friendly | Offer better long-term value in harsh environment |
Visual and Aesthetic Differences | Shiny and smooth | Dull grey and a little rough |
Application | Indoor machinery, Ligh-duty uses, Budge-friendly projects | Outdoor machinery, Marine and coastal uses, Heavy-duty industrial equipment |
Zinc Plated VS Galvanized
What Does Galvanised Mean?
Galvanization involves applying a protective zinc coating to steel or iron to prevent rust. The most common method is hot-dip galvanizing, where metal parts are submerged in molten zinc. Zinc plating (electro-galvanizing) uses electricity to apply zinc, offering some rust protection but with a thinner, less durable coating. Zinc plating is cheaper and easier to weld.
When choosing, note that 'galvanized' doesn’t always mean 'hot-dip galvanized.' Electro-galvanizing is another term for zinc plating. Ensure the product is hot-dip galvanized for better rust resistance.
What Are The Different Galvanisation Processes?
Whether the steel is to be hot dip galvanized or zinc plated it is prepared in a similar way. The steel is cleaned to remove all oils, paint, grease, mill scale (small flakes of metal), and rust in a bath of acid.
Steel, when being hot dip galvanized is dipped into a 450°C bath of molten liquid zinc. The steel and the liquid zinc bond together because of the high temperature. The steel and the zinc become one. Hot dip galvanizing requires a minimum thickness of 45μm (.045mm) and goes beyond 100μm (.1mm).
Zinc plating, on the other hand, is immersed in a cold chemical solution of zinc and uses an electrical current to apply a layer of zinc. The thickness of the coating is measured in microns or micrometers (μm). Zinc plating requires a minimum thickness of 5μm (.005mm) and a maximum of 25μm (.025mm). It would become too technical and expensive to coat the steel any thicker than this.
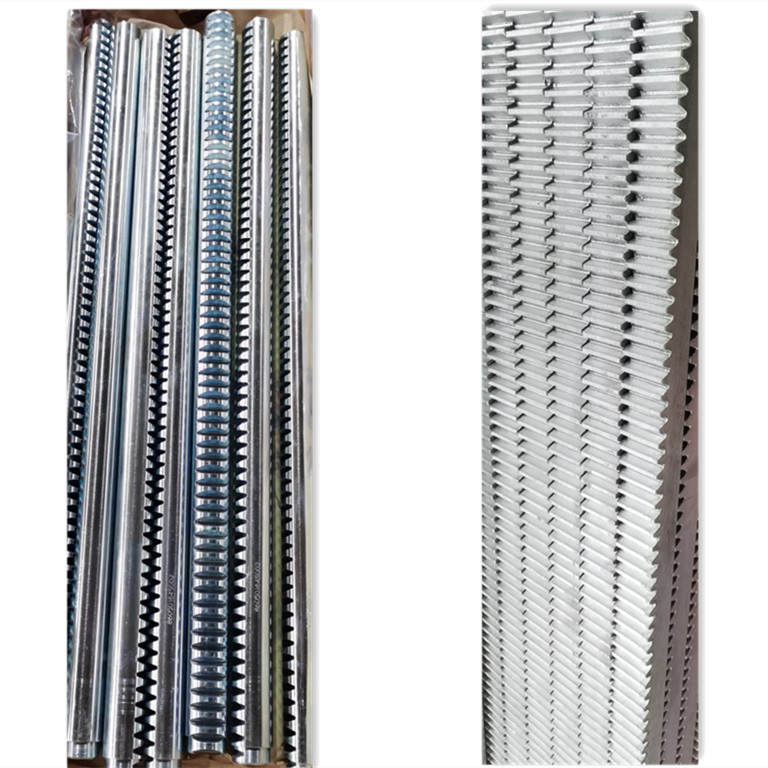
Zinc Plated on the Left vs Hot Dip Galv on the right
CTS Roller Chain Selection
ANSI roller chains follow American standards, measured in inches. Common in North America, they are strong and widely used in industrial and agricultural machinery.
Metric roller chains, measured in millimeters, follow international standards. Popular in Europe, they are used in industries requiring global metric compatibility.
CTS® | Reliable Roller Chains Supplier
For over 14 years, CTS® has dedicated itself to crafting top-quality roller chains and power transmission components. If you're seeking a reliable Roller Chain solution, look no further. With a full range of ANSI Roller Chains and Metric Roller Chains at your disposal, our experienced technicians are ready to assist you in finding the perfect fit for your needs.
If you have any questions, please feel free to contact us, CTS® professional technicians will be happy to help you!