Double Roller Chain – Types, Applications & Selection Guide
What Is Double Roller Chain?
Double roller chains (also called dual roller chains or duplex chains) are a heavy-duty power transmission component designed to handle higher loads than standard single-strand chains. By using two parallel rows of rollers, these chains distribute stress evenly, making them ideal for demanding industrial, agricultural, and automotive applications. Popular models like ANSI 40-2 and ISO 10B-2 are widely used in conveyor systems, heavy machinery, and the agriculture industry.
Why Choose Double Roller Chains ?
Higher Load Capacity: Dual rollers reduce wear under heavy loads.
Extended Lifespan: Robust construction resists elongation and fatigue.
Versatility: Compatible with multi-strand sprockets for complex setups.
Double Roller Chain Size
Tips: Always match your roller chain to the chain sprocket's pitch and tooth count (e.g., 40-2 chain pairs with a 40-2 sprocket).
How Double Roller Chains Work
Double starnd roller chains consist of inner plates, outer plates, pins, bushings, and two rows of rollers. The duplex design allows the chain to engage with sprockets more smoothly, reducing friction and noise. Unlike single roller chains, double roller chains are built for high-torque applications, such as mining equipment or construction machinery.
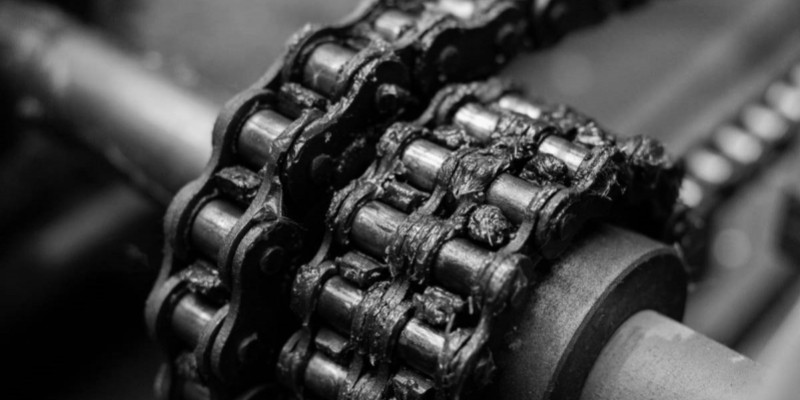
Applications of Double Roller Chains
Thanks to double roller chains' high durability and reliability, they are used in a variety of industries:
Industrial Machinery – Used in conveyors, crushers, and material-handling equipment.
Agriculture – Common in combine harvesters, balers, and tractors.
Automotive – Used in engine timing systems and transmission drives.
Food & Beverage Industry – Stainless steel versions are used in food processing and packaging lines.
How To Choose the Right Double Roller Chain
1) Select the Right Roller Chain Size
Choose a chain size based on ANSI (#40-2, #50-2, #60-2, etc.) or ISO (08B-2, 10B-2, 12B-2, etc.) standards.
For heavier loads, use heavy-duty versions (e.g., 40H-2, 50H-2).
2) Check Roller Chain Load Capacity & Strength
Tensile Strength – Ensures the chain can handle heavy loads.
Working Load Limit (WLL) – Pick a chain with a higher WLL than the actual load.
Shock Resistance – Needed for high-impact applications like heavy machinery.
3) Choose the Right Chain Material
Carbon Steel Roller Chain – Strong & cost-effective for general industrial use.
Stainless Steel Roller Chain – Best for food processing, marine, and pharma (corrosion-resistant).
Nickel-Plated Roller Chain – Good for high-humidity or chemical exposure.
Self-Lubricating Roller Chain – Ideal for high-speed machines, reducing wear & maintenance.
4) Consider Environmental Factors
High Temperatures – Use nickel-plated or stainless steel chains.
Dusty/Abrasive Areas – Choose sealed or self-lubricating chains.
Wet/Corrosive Environments – Stainless steel or zinc-coated chains prevent rust.
5) Ensure Chain Sprocket Compatibility
Match the chain pitch and tooth profile with the correct sprocket size. Keep sprockets aligned to reduce wear and extend chain life.
CTS | Professional Roller Chain Manufacturer
CTS®-ChinaTransmissionS is a professional roller chain supplier with over 14 years in the power transmission industry.
As a professional roller chain supplier, our experienced technical team continuously learns the latest manufacturing technology. It would be better for you to build long-term and stable cooperation with us, and we can provide priority service and fast response for the first time.
We offer various industrial chain options: roller chains, conveyor chains, stainless steel chains, heavy-duty roller chains, double-pitch roller chains, roller chain attachments, etc.
If you have any questions about roller chains, please contact us.